Forklifts and Warehouse Safety: What You Need to Know
Forklifts are essential tools in warehouse operations, enabling the efficient movement of heavy materials. However, their immense power and size also pose significant safety risks. In New Zealand, according to WorkSafe, forklift incidents are a leading cause of injuries in the warehousing and storage industry. Understanding the impact of forklifts on warehouse & pallet racking safety and by implementing best practices can significantly reduce accidents and improve overall operational efficiency. Not only this, but, conducting regular racking inspections ensures your warehouse and its staff are kept safe from damaged pallet racking as well as injury.
“At Cemac | Dexion, we encourage businesses to keep up with annual racking inspections to prevent injuries and warehouse damage. If your racking has been hit by a forklift, contact us and we can come and assess the damage” Scott Shirley, Managing Director.
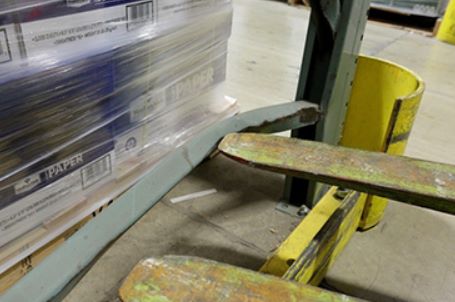
Forklifts and the Hidden Threat: Damaged Racking
Forklifts are the workhorses of warehouses, but their immense power can also pose a hidden threat: damage to storage racking. These seemingly minor bumps and scrapes from forklift collisions can have serious consequences.
Here’s how forklift interactions can damage racking:
Collisions with Uprights: Accidental contact with the vertical supports (uprights) of the racking system can cause dents, bends, or cracks. This weakens the overall structure and reduces its load-bearing capacity.
Impact on Beams and Braces: Collisions with horizontal beams or diagonal braces can misalign components, loosen connections, or even cause warping. This can lead to uneven load distribution and potential collapse.
Fork Impacts: Protruding forks accidentally hitting the racking can cause localized damage, compromising the integrity of individual components.
These seemingly minor injuries to the racking system can have cascading effects:
Racking Failure: Over time, accumulated damage can lead to a catastrophic racking failure. A single compromised upright or beam could give way under the weight of stored goods, causing a domino effect that brings down entire sections of racking.
Product Damage: Collapsed racking can crush and damage stored products, resulting in significant financial losses.
Worker Injuries: In the worst-case scenario, a racking failure can cause serious injuries or even fatalities to warehouse personnel working near or underneath the damaged structure.
Racking Inspections: A Proactive Approach to Safety
Regular inspections of your pallet racking system are crucial to prevent these dangers. Here’s how inspections help:
Early Detection: Trained inspectors can identify minor damage before it progresses into a major safety hazard. Early intervention allows for repairs or replacements to be made, preventing catastrophic failures.
Maintaining Structural Integrity: Inspections ensure that the racking system maintains its designed load capacity. This protects both workers and inventory by ensuring the safe storage of goods.
Peace of Mind: Proactive inspections provide warehouse managers with peace of mind, knowing they’ve taken steps to create a safe working environment and minimize the risk of costly accidents.
By incorporating regular racking inspections alongside proper forklift operation protocols, warehouses can create a safer and more efficient environment for everyone. It’s a small investment that yields significant returns in terms of worker safety, product protection, and overall operational success.
Repeated Brushing: Frequent friction between pallets and racking components (beams, braces) during placement and retrieval can cause deformation over time, impacting the overall stability of the system. Factors like narrow aisles, improper pallet angles, and oversized/heavy pallets can increase this risk.
Wear and Tear: Over time, everyday use can lead to gradual wear and tear on components, like bolt loosening or connection fatigue.
Warehouse Traffic: Collisions with racking systems by moving vehicles (forklifts, pallet jacks) other than planned operations can cause damage.
The biggest threat from forklift impacts is that the damage often goes unnoticed. Minor dents, cracks, or misalignments might not be readily apparent, but they can significantly weaken the racking system. This hidden damage can silently progress until one day, under the weight of stored goods, the entire racking system fails catastrophically.
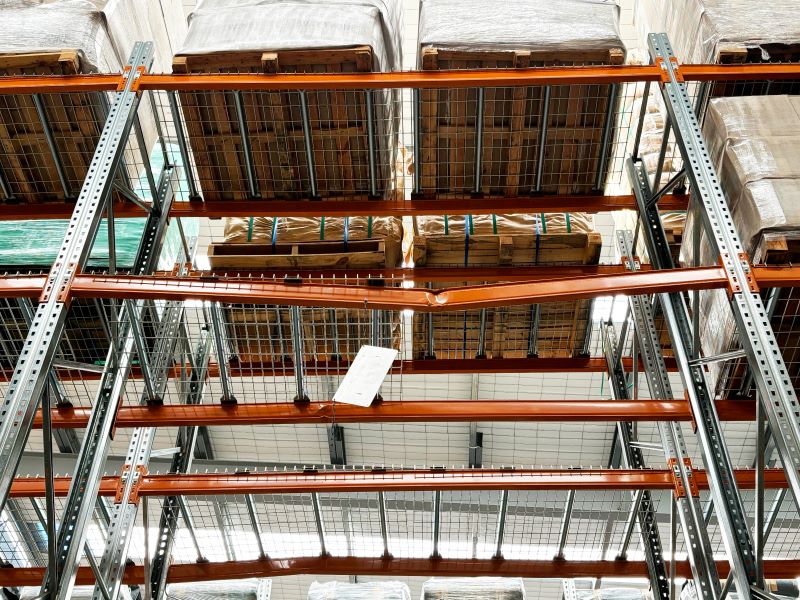
Preventive Measures:
Protect Uprights: Install guards like bollards or rails at the base of uprights to deflect impacts and end frame protection is also mandatory under the standard (As4084-2023)
Beam Visibility: Use brightly coloured beams (yellow or orange) to enhance visibility for forklift drivers. At Cemac, we are distributors & installers of orange Dexion Racking, and racking protectors which ensures that the beams are very visible.
Encourage Reporting: Establish a “no-repercussions” policy for workers to report any impacts on the racking.
Regular Inspections: Conduct frequent visual inspections (Inspections should be conducted at intervals not exceeding 12 months by competent inspectors. However, additional inspections can be scheduled based on the company’s preference) and involve certified engineers for less frequent, in-depth assessments.
Internal monthly inspections are also required which can be carried out by your own team and talked to someone to get the guidelines required.
Clear Signage: Post rack load capacities and operational guidelines prominently are also mandatory.
Maintain Rack Integrity: Avoid altering rack components without professional assistance.
Proper Pallet Use: Utilise well-maintained pallets designed for the specific racking system and loads.
Safe Loading Practices: Ensure proper pallet placement, balance, and securement to prevent tipping or overhang.
Adequate Space: Provide ample space (below 6m a min 100 mm and above 6m that number increases to 125mm) above loads for safe forklift manoeuvring.
Final Notes
Implementing strong safety measures and best practices for forklift use is crucial for maintaining a safe and efficient warehouse environment. By prioritising regular training for operators, proper maintenance of equipment, adherence to established safety protocols, and regular inspections of your pallet racking system, you can mitigate the risks associated with forklifts. This not only ensures the well-being of employees but also allows for smooth operation and optimal productivity in your warehouse activities. Ultimately, prioritising forklift safety creates a win-win situation for both employee safety and operational success.
At Cemac our Team of Installers have all completed their forklift training and have obtained licenses to safely operate forklifts in our warehouse and on site. Pallet racking inspections should be conducted at intervals not exceeding 12 months by competent inspectors, however, additional inspections can be scheduled based on the company’s preference, we have approved inspectors who are capable of providing comprehensive storage racking inspections, so call us today if you are in need a check up or for your annual check.
Meet our team of installers
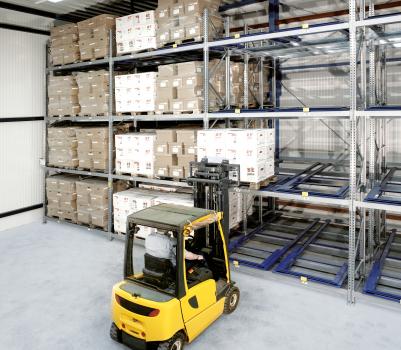
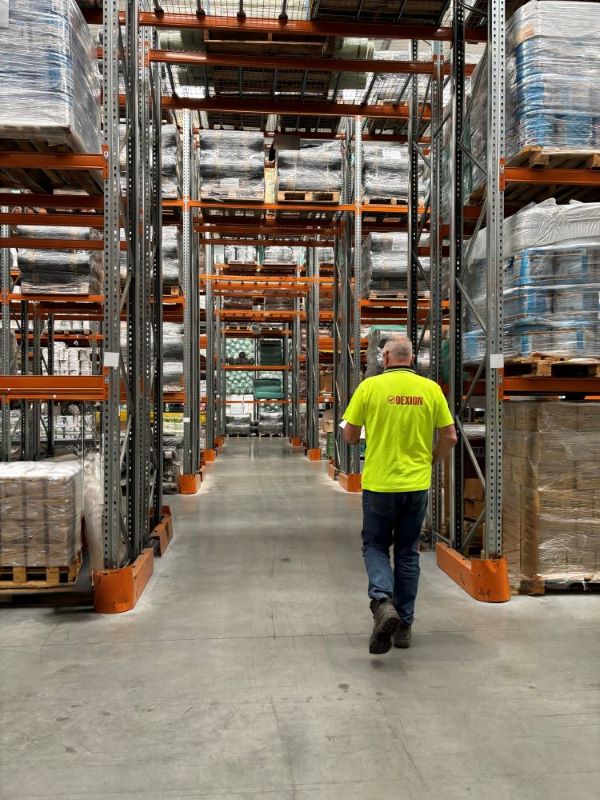
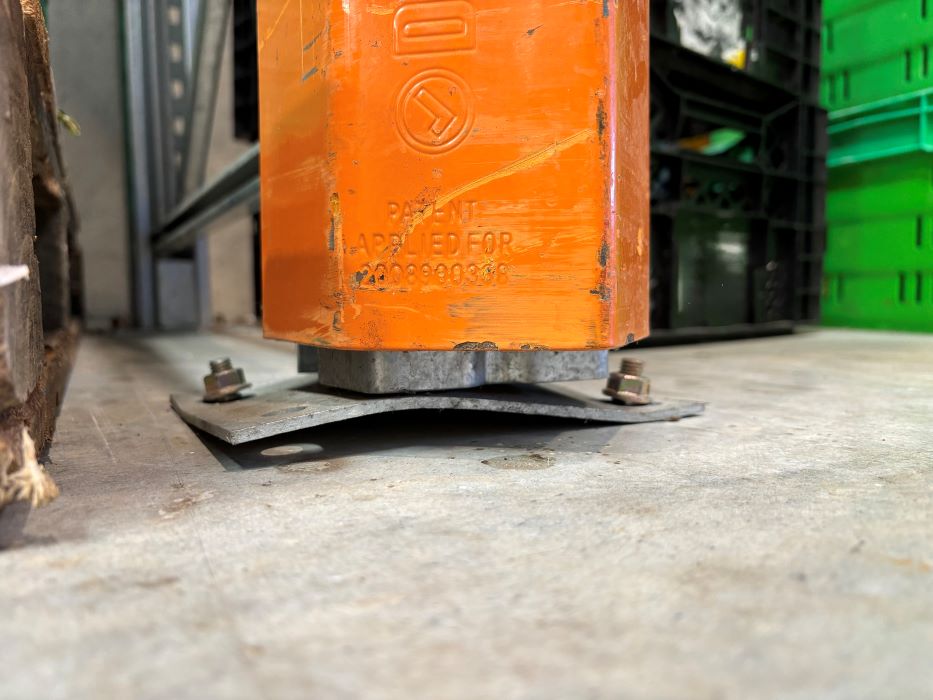
Why not ensure peace of mind by having competent inspectors evaluate your racking?
Get in touch today
Phone: 078395145
Email: info@cemac.nz
Website: cemac.nz